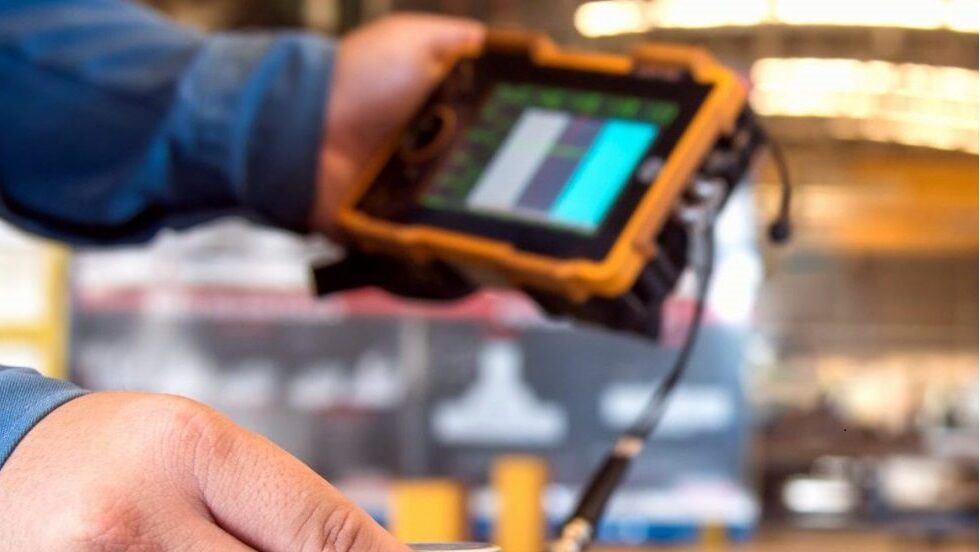
El Caso: Análisis de fallos en componentes:
El análisis de fallos en componentes es fundamental en el área de mantenimiento, ya que permite una gestión eficiente de las variables operativas de los equipos. Para ello, es clave contar con personal especializado y establecer programas de monitoreo basados en técnicas predictivas.
Estas estrategias permiten identificar fallas potenciales, definir planes de acción efectivos, extender la vida útil de los componentes y mejorar la confiabilidad operativa de la maquinaria.
- Tipo de Aceite Utilizado: SAE 60 – ISO 320
- Capacidad de Almacenamiento de Lubricante: 225 Galones
- Horas de Operación del Conjunto: 3850.5 Horas
- Síntoma de Falla: Partículas de fierro en tapones de inspección
- Valor monetario Aproximado del Conjunto: $150,000.00
- Frecuencia de Cambio del Lubricante: 4000 horas
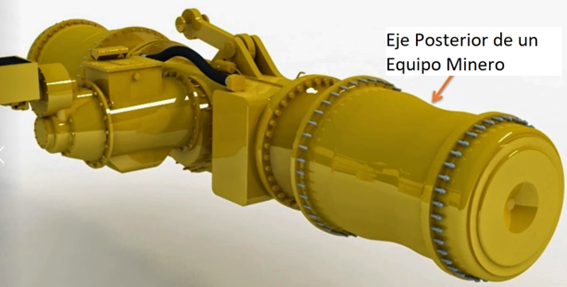
Técnicas Predictivas para el Diagnóstico de Fallos en Equipos Industriales
Para cumplir con este objetivo, se han establecido las siguientes técnicas predictivas como fuentes de información del eje posterior de este equipo minero:
- Muestreo de Tapones de Inspección Magnéticos
- Análisis de Lubricantes
- Muestreo de Filtro
- Análisis de Cargas en el Eje Posterior
Identificación del Problema
El síntoma principal de la falla se detectó mediante el análisis de las muestras repetitivas de los tapones magnéticos. Estos mostraban una concentración elevada de partículas ferrosas.
Además, los análisis periódicos del lubricante evidenciaron un aumento significativo en la concentración de Fe y PQ en las últimas dos semanas, superando los valores críticos establecidos.
Ante esta situación, se programó la inspección y evaluación de los componentes del eje posterior, específicamente en los Mandos Finales y el Diferencial. Sin embargo, el daño observado durante la inspección llevó a la necesidad de un Mantenimiento Correctivo No Programado, lo que implicó el reemplazo de los componentes afectados.
Evidencias del Análisis
Los resultados obtenidos en las inspecciones se detallan a continuación:
- Muestras sucesivas de tapones magnéticos con alta concentración de partículas ferrosas.
- Análisis de lubricante, evidenciando niveles elevados de Fe y PQ.
- Desgaste en componentes clave, como:
- Dientes de la corona
- Pista externa del rodamiento del piñón
- Rodamiento del piñón
- Topes externos y Trust Washer del mando final derecho
Esta información respalda la necesidad de aplicar estrategias predictivas más avanzadas para prevenir fallos similares en el futuro.
Resultados de Tapones Magnéticos en muestras sucesivas.
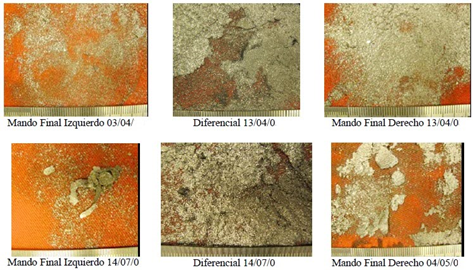
Resultados del Análisis de Lubricantes en Equipos Industriales
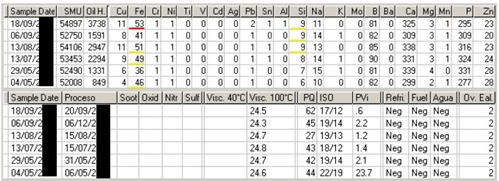
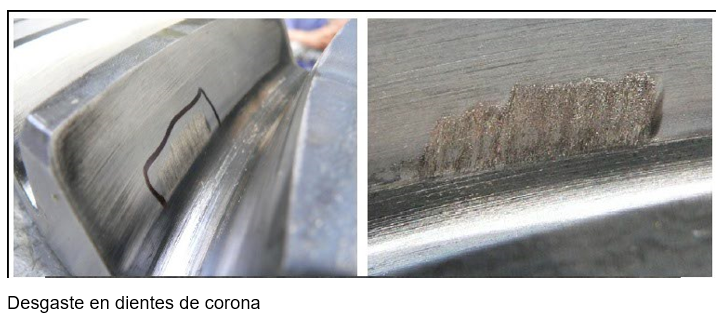
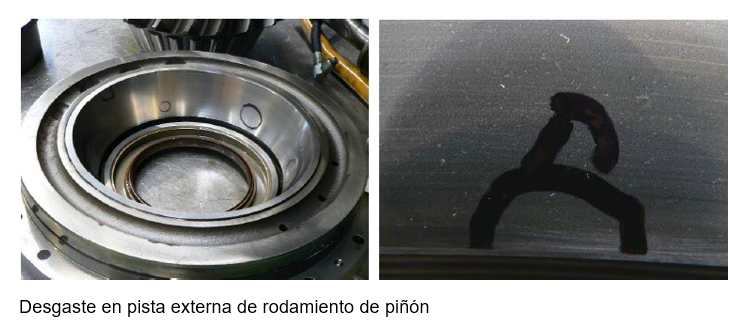
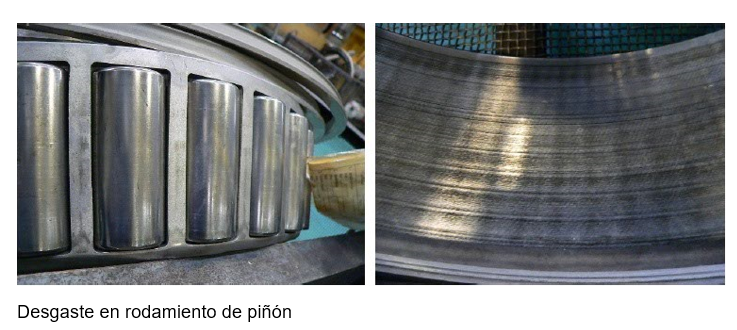
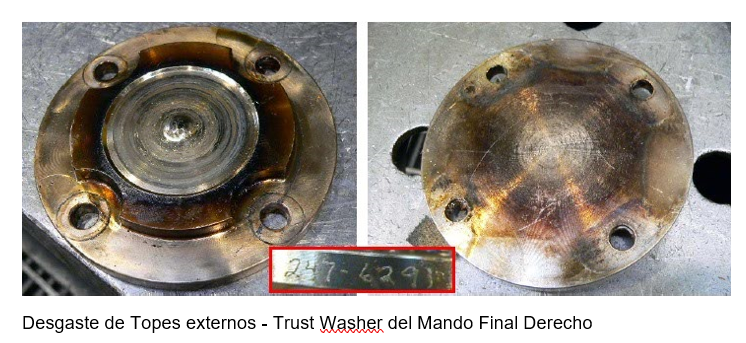
Estrategias de Análisis de Fallos en Componentes Industriales
Conclusiones y Oportunidades de Mejora en el Diagnóstico Predictivo
De las cuatro técnicas predictivas utilizadas para identificar la falla potencial en este conjunto de componentes, la más determinante ha sido el muestreo de tapones magnéticos, específicamente cuando alcanzó su etapa de condición crítica.
Las otras tres técnicas—análisis de lubricantes, muestreo de filtro y análisis de cargas—fueron consideradas complementarias para la toma final de decisiones. En particular, el análisis de lubricantes resultó clave debido a la detección de niveles elevados de Fe (hierro en ppm) y PQ (concentración de partículas ferrosas).
Oportunidades de Mejora
Si bien la decisión final puede estar sujeta a políticas internas del área de mantenimiento, es fundamental optimizar el proceso de análisis del equipo de monitoreo de condiciones y confiabilidad. Esto permitirá actuar dentro del intervalo P-F, minimizando daños internos y optimizando la respuesta ante fallos.
Algunas estrategias de mejora incluyen:
- Incorporar técnicas predictivas adicionales, como el Análisis Ferrográfico en filtros y tapones, para identificar el tipo de partículas y su mecanismo de desgaste.
- Mejorar la interpretación de los reportes de análisis de lubricantes, considerando todos sus parámetros de evaluación.
- Implementar un Programa de Análisis de Lubricantes, que integre estos procesos y optimice la toma de decisiones en mantenimiento.
Estas mejoras fortalecerán la estrategia de mantenimiento predictivo, reduciendo costos y prolongando la vida útil de los componentes críticos.
Factores Críticos en el Análisis de Fallos de la Industria
Las evidencias observadas indican que la generación de contaminación interna (partículas ferrosas) fue causada por el desprendimiento de material en las zonas de contacto de la corona y el piñón de ataque del diferencial. Este fenómeno ocurrió en su etapa de mortalidad infantil (Patrón de falla F), lo que provocó un desgaste de tipo adhesivo entre ambos materiales.
Es altamente probable que la falla progresiva del diferencial (degradación de su función) haya generado un empuje axial del semi-eje del mando final derecho, ocasionando un contacto directo con el tope externo. Como consecuencia, se produjo una mayor cantidad de partículas ferrosas, detectadas posteriormente en los tapones magnéticos y en el reporte de análisis de lubricante.
Recomendaciones en Análisis de fallos en componentes
Para evitar fallas similares en el futuro, se recomienda:
- Realizar un monitoreo más preciso en la fase inicial de operación, para identificar signos tempranos de desgaste adhesivo.
- Implementar análisis ferrográficos periódicos, para caracterizar las partículas ferrosas y determinar su origen exacto.
- Ajustar los parámetros de inspección de lubricantes, enfocándose en tendencias de concentración de Fe y PQ.
- Optimizar el diseño o condiciones operativas, si es recurrente el desgaste prematuro en estos componentes.
Estas acciones contribuirán a mejorar la confiabilidad del diferencial y reducir costos de mantenimiento correctivo.
Análisis de fallos en componentes: Optimización del Proceso de Análisis
Para mejorar la precisión en la detección de fallas potenciales, es fundamental fortalecer el proceso de análisis basado en el reporte de análisis de lubricantes. Esta técnica predictiva ofrece una evaluación detallada del estado del componente al medir más de 40 parámetros, lo que la convierte en una herramienta superior respecto a otras metodologías.
Acciones Claves para la Mejora
Integración de Análisis Avanzado
- Implementar algoritmos de tendencia que correlacionen múltiples parámetros en el tiempo.
- Priorizar la detección de elementos críticos como Fe (Hierro en ppm) y PQ (Índice de partículas ferrosas).
Capacitación del Personal de Monitoreo
- Mejorar la interpretación de los reportes mediante entrenamientos especializados.
- Fomentar la detección temprana de anomalías dentro del intervalo P-F.
Uso Complementario de Técnicas Predictivas
- Incorporar análisis ferrográfico en filtros y tapones para identificar el mecanismo de desgaste.
- Comparar datos del análisis de lubricantes con vibraciones y termografía para validación cruzada.
Optimización de Frecuencia de Muestreo
- Ajustar los periodos de análisis según el historial de fallas y condiciones operativas.
- Implementar un sistema de alerta temprana basado en desviaciones críticas.
Estas acciones permitirán una identificación más precisa y anticipada de fallas potenciales, minimizando costos de mantenimiento correctivo y optimizando la vida útil de los componentes.
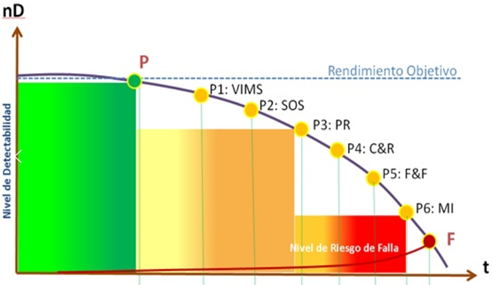
Desarrollar un proceso de análisis de modos de falla del conjunto del tren posterior, tomando como referencia la Metodología del Mantenimiento Centrado en la Confiabilidad RCM mediante el cual se determinarán de manera efectiva las estrategias de mantenimiento adecuados así como los planes de acción que deben realizarse para administrar cada modo de falla, con lo que se incluyen: Frecuencias de inspección, establecer límites de alarma para cada caso, técnicas predictivas más convenientes, rediseño de elementos mecánicos, frecuencia de cambio de lubricantes, entre otros.
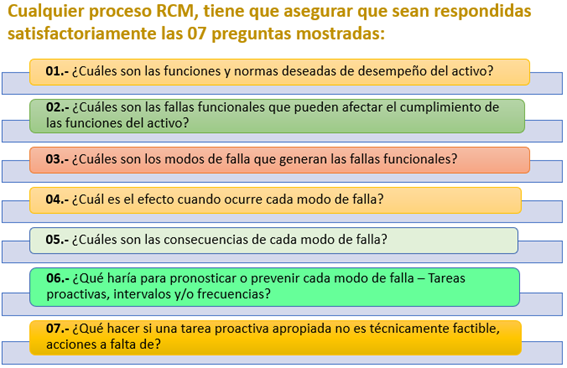
Análisis de fallos en componentes: Programa de Análisis de Lubricantes para la Industria
Para optimizar la detección de fallas y extender la vida útil de los componentes, se debe establecer un Programa de Análisis de Lubricantes basado en los principios del RCM (Mantenimiento Centrado en Confiabilidad). Este programa debe contemplar los siguientes aspectos clave:
1. Control de Contaminación
- Implementar medidas para minimizar partículas internas y externas en el sistema.
- Usar filtros de alta eficiencia y monitorear su estado periódicamente.
2. Interpretación de Mecanismos de Desgaste
- Aplicar análisis ferrográfico para identificar la naturaleza de las partículas.
- Diferenciar entre desgaste normal y señales de falla potencial.
3. Gestión del Aceite Lubricante
- Definir y controlar el tipo de aceite utilizado según las especificaciones del fabricante.
- Establecer una frecuencia óptima de cambio de aceite basada en la condición real del lubricante.
4. Frecuencia de Muestreo y Límites de Alarma
- Determinar puntos de muestreo estratégicos para obtener información representativa.
- Definir límites de alarma para elementos críticos como Fe (ppm) y PQ (Índice de partículas ferrosas).
5. Compromiso Gerencial y Sostenibilidad
- Integrar el programa con el plan estratégico de mantenimiento.
- Asegurar el apoyo de la gerencia y línea de mando para garantizar recursos y continuidad.
- Promover la colaboración entre el área de monitoreo de condiciones y las demás áreas operativas.
Este enfoque garantizará decisiones basadas en datos confiables y en tiempo real, optimizando los recursos y reduciendo costos de mantenimiento correctivo.
¡¡¡Esperamos sus comentarios para enriquecer el análisis de este caso, confiamos en que sea de su provecho!!!