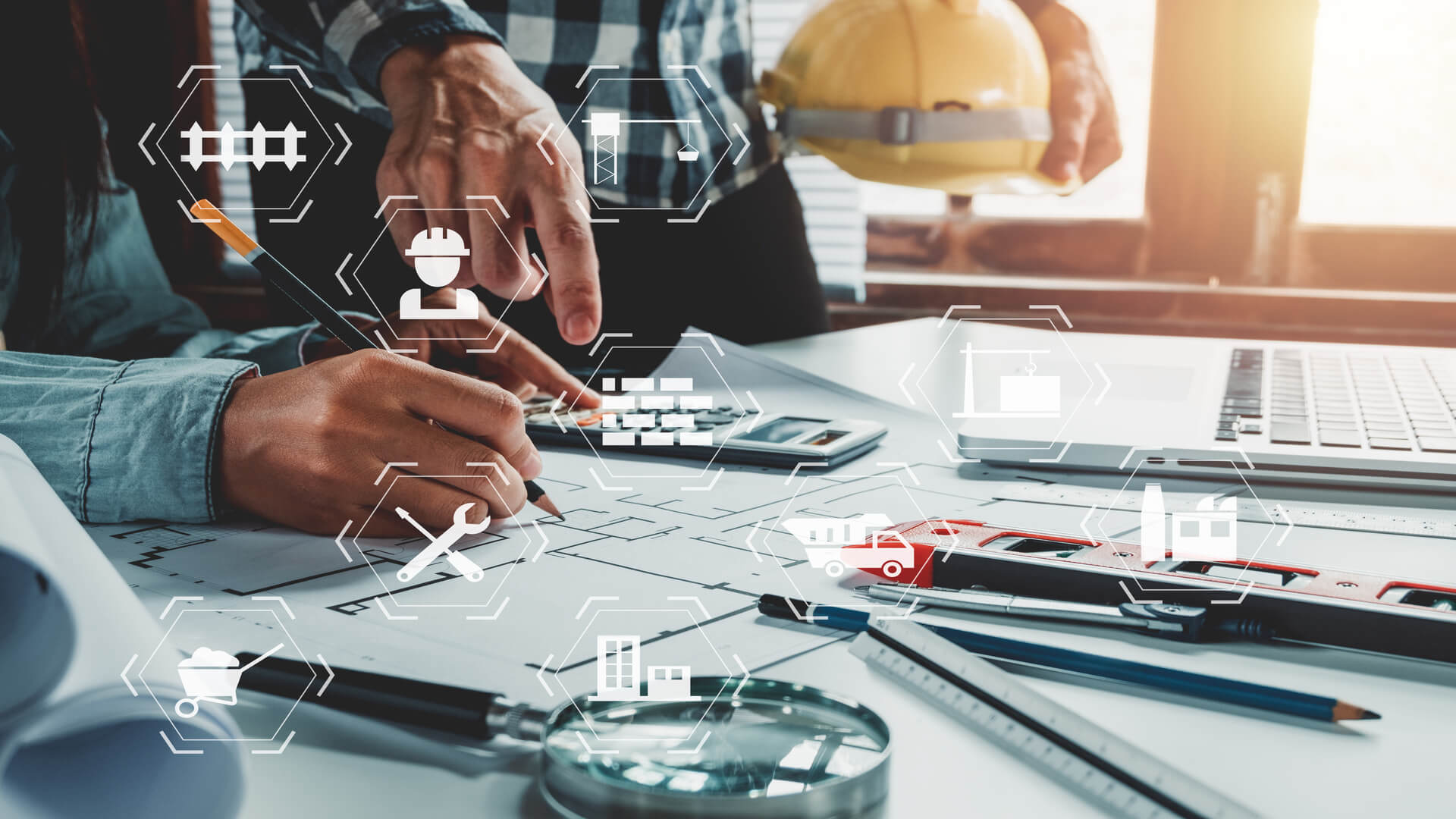
Recordemos que las estrategias de mantenimiento conocidas y tradicionales son: Mantenimiento Correctivo, Mantenimiento Preventivo y el Mantenimiento Predictivo; cada una de estas estrategias forma parte de las actividades diarias del departamento de Mantenimiento de cualquier Empresa, donde, dependiendo de la complejidad de los equipos y/o activos administrados dichas estrategias serán implementadas con mayores recursos humanos, técnicas, métodos, equipos y/o herramientas. Estas estrategias podrían tener una variedad de nombres, sin embargo, decantan sobre los mismos conceptos.
El libro del Mantenimiento Centrado en la Confiabilidad RCM-II utiliza nombres alternativos para definir dichas estrategias siendo éstas:
- Correr hasta la falla = Mantenimiento Correctivo
- Tareas de sustitución cíclica = Mantenimiento Preventivo especializado
- Tareas de reacondicionamiento cíclico = Mantenimiento Preventivo rutinario
- Tareas a condición = Mantenimiento Predictivo
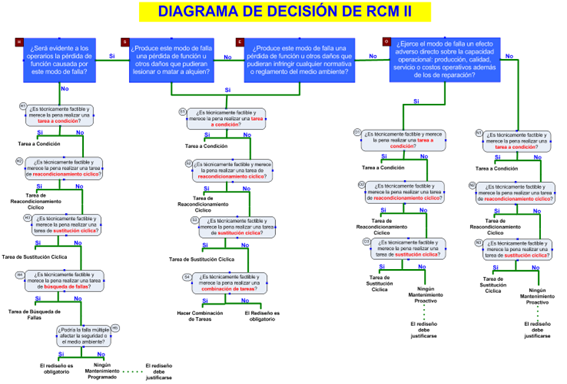
Una de las preguntas más frecuentes del profesional de mantenimiento de las áreas de: Gerencia, Superintendencia, Supervisión, Planeamiento, Programación y Confiabilidad es:
¿Cómo evaluar la factibilidad económica de una estrategia de mantenimiento?
Esto, con la finalidad de mejorar la gestión de los activos de la empresa, reduciendo los costos operativos del área y enfocando eficientemente las actividades de mantenimiento de acuerdo a la criticidad de los modos de falla recurrentes durante el proceso de producción.
A. Evaluación económica entre una estrategia de Mantenimiento Preventivo y Mantenimiento Correctivo
La figura 02, muestra la fórmula que nos permite comparar entre realizar una estrategia de mantenimiento preventivo u optar por un mantenimiento correctivo, es decir: “Correr hasta la falla” en función del impacto económico por el modo de falla predominante.
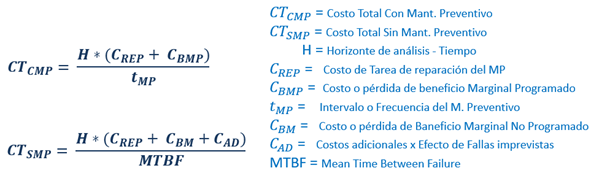
En esta evaluación económica, con resultados en unidades monetarias ($$$), es importante registrar adecuadamente cada uno de los factores indicados, tales como: Costos de reparación, impacto monetario del beneficio marginal, costos adicionales de las consecuencias de las fallas y las frecuencias de mantenimiento preventivo. Toda esta información debe estar correctamente registrado y categorizado en las órdenes de trabajo de las actividades de mantenimiento y de ser posible en un sistema informático o ERP que pueda manejar la empresa.
Es necesario también el de registrar el MTBF = Tiempo promedio entre fallas, el cual vendría a ser parte de un registro estadístico que nos permite hacer inferencia para aproximar el comportamiento general de los equipos que son administrados por el área de mantenimiento.
El horizonte de tiempo “H”, debe ser considerado por cada profesional de mantenimiento de acuerdo al contexto operacional de sus equipos, y considerando un escenario de corto, mediano y largo plazo. Se podrían realizar evaluaciones anuales, si los modos de falla tienen alta frecuencia de recurrencia, o cada 5 años para tener una mejor visión de los diferentes escenarios que se podrían presentar durante el periodo de operación de los equipos.
Planteamos el siguiente caso como parte de la aplicación de la fórmula indicado en la figura 02 con la finalidad de obtener algunas conclusiones significativas:
Caso 01
«Una máquina posee un rodillo de imprimación de adhesivo cuyo modo de falla dominante es «desgaste de su superficie de contacto con el producto». Cuando la superficie se encuentra con un alto nivel de deterioro, el agregado de adhesivo resulta insuficiente lo que provoca pérdidas por desechos de producción.
La identificación del desvío en los rodillos es evidente al menos una vez por turno, dado a que ese es el intervalo de toma de muestras efectuado por el departamento de calidad. Esto lleva a que en el peor de los casos, se deba perder la producción completa de un turno de 8 horas de etiquetado.
La condición más desfavorable (materiales e insumos por 8 horas) no afecta las ventas debido al nivel de pre-stock elaborado y a que la velocidad de la máquina permite recuperar el volumen de producción perdido en el próximo turno. La pérdida en materiales e insumos (para 8 horas de producción) estimada es de $ 7200.00.
Se sabe que los rodillos de este tipo, en la máquina referida, nunca dejan de aportar correctamente el adhesivo antes de los 6 meses de funcionamiento continuo. Además de lo comentado por el proveedor de los rodillos, se pudo realizar la comprobación empírica en la planta de etiquetado.
Sin embargo, un estudio estadístico sobre 500 rodillos realizado hace unos años, arrojó que el MTBF para el modo de falla indicado es de 12 meses.
Si la tarea de mantenimiento preventivo le cuesta a la compañía un total de $ 1340.00 cada 6 meses y puede planificarse en turnos de baja producción, calcular si la misma resultará conveniente cuando hayan transcurrido 4 años de operación.»
El primer caso, solicita evaluar si es conveniente realizar una estrategia de mantenimiento preventivo o correctivo, para ello el periodo de evaluación es de 4 años de producción
La resolución al problema se puede obtener al identificar correctamente los factores que componen ambas fórmulas:
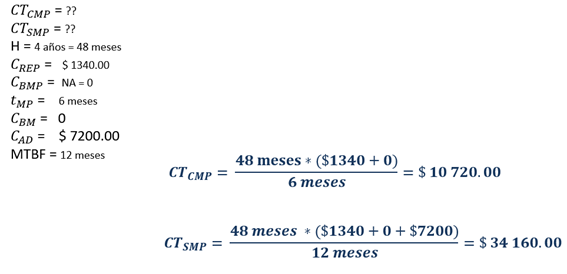
El resultado nos indica que realizando las actividades de mantenimiento se obtiene un gasto de $ 10 720.00 en comparación de un mantenimiento correctivo cuyo gasto llegaría hasta los $ 34 160.00 por lo que la selección de la estrategia de mantenimiento preventivo es la mas adecuada desde el punto de vista económico.
Podríamos aplicar alguna estrategia de gestión de mantenimiento al Caso 01 planteado, tal como lo indicamos en el Caso 02 y comparar los resultados económicos entre ambas estrategias de mantenimiento.
Caso 02
«Sea el mismo ejemplo anterior, sólo que ahora el departamento de calidad realiza los controles a intervalos de 1 hora. Así la consecuencia del modo de falla puede ser identificado en el peor de los casos una hora después de sucedido. Calcular los costos totales con y sin mantenimiento preventivo.»
En el segundo caso, se requiere que un inspector del área de mantenimiento realice inspecciones con una frecuencia de una hora con la finalidad de identificar problemas de operación del equipo, por ello el monto de los costos adicionales será menor debido a que las pérdidas de los materiales serán solo de hasta una hora de producción en comparación con las 8 horas de producción del Caso 01.
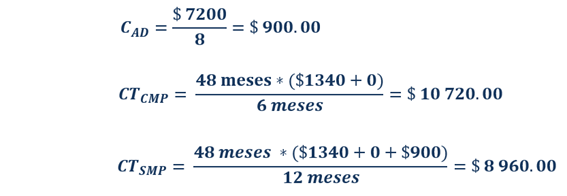
Evidentemente para el caso 02 será más conveniente “correr hasta la falla” debido a que los costos totales son menores que si se aplicase una estrategia de mantenimiento preventivo.
Sin embargo, se tendría que considerar, el costo del personal que realizará las inspecciones rutinarias de una hora, si se cuenta con el personal de calidad disponible sería solamente una cuestión de orden y planificación.
Sobre este Caso 02 también se podría aplicar otra estrategia de gestión de mantenimiento el cual es planteado en el Caso 03 para buscar otras alternativas que nos permitan seleccionar adecuadamente la estrategia de mantenimiento.
Caso 03
Considere el mismo ejemplo anterior, pero luego de grandes esfuerzos en conjunto con el proveedor de los rodillos se logró que no sucedan fallas antes de los 11 meses. Calcular nuevamente la conveniencia de aplicar el mantenimiento preventivo.
Para este tercer caso, se debe presentar mejoras en el diseño, manufactura o fabricación de las piezas mecánicas con la finalidad de incrementar su confiabilidad, el cual deberá estar respaldada en pruebas de campo dentro del contexto operativo en el cual se desempeñan.
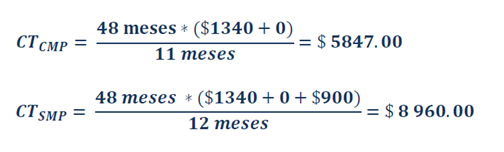
Se puede apreciar que será más conveniente aplicar una estrategia de mantenimiento preventivo en comparación de una de mantenimiento correctivo por tener menores costos operativos en el periodo de evaluación planteada.
De acuerdo a lo analizado se pueden desprender las siguientes conclusiones:
- El caso 01, muestra el estado inicial en el que se puede encontrar el área de mantenimiento con la finalidad de evaluar los costos reales que impactan al proceso.
- El caso 02, plantea una alternativa de mejorar el cual consiste en incrementar la frecuencia de inspección con la finalidad de identificar la falla oportuna del equipo.
- El caso 03, plantea una mejora en la confiabilidad de los rodillos de imprimación que incremente las horas de operación, con lo que se obtienen menores costos operativos para el funcionamiento del equipo con lo que podemos resaltar que los mayores esfuerzos del área de mantenimiento deben estar enfocados en incrementar la confiabilidad de los elementos, equipos y/o sistemas.
- Considerar que, para aplicar una estrategia de mantenimiento, es necesario que los tiempos promedios entre fallas (MTBF) sigan una distribución normal, caso contario las conclusiones derivadas de los resultados podrían ser imprecisas.
B.- Evaluación económica entre una estrategia de Mantenimiento Predictivo y Mantenimiento Correctivo
La figura 03, muestra la fórmula que nos permite comparar entre realizar una estrategia de mantenimiento predictivo o permitir un mantenimiento correctivo, es decir: “Correr hasta la falla”
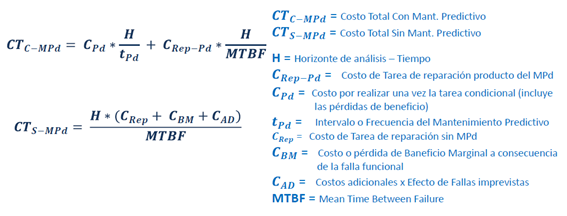
De acuerdo a la fórmula propuesta, será necesario conocer el costo de la técnica predictiva ( ) así como la frecuencia con la que será realizada ( ), además cada vez que se detecte el parámetro de evaluación fuera de los límites de aceptación será necesario conocer el costo que será necesario para realizar el correctivo necesario ( ). Todo esto deberá ser evaluado en el horizonte de tiempo determinado por el departamento de mantenimiento (H). El MTBF es un parámetro estadístico importante para estimar las veces que será probable que ocurra el modo de falla crítico que está siendo evaluado.
La aplicación de
esta evaluación económica la podemos describir en el siguiente caso:
CASO 04
Un reductor de transmisión de potencia contiene para su lubricación una carga con 90 litros de aceite. El mismo opera continuamente y cuenta con las protecciones necesarias contra la contaminación de polvo y otras sustancias. Un código ISO de limpieza por debajo de 18/16/14 garantiza un buen estado de lubricación evitando daños en la película lubricante y por consiguiente en sus partes mecánicas. Si en algún caso se verifica que el nivel de limpieza excede el valor fijado como límite, se procede a una limpieza (filtrado) por recirculación paralela que ocasiona un gasto de $ 1250.00 (incluye mano de obra, filtros, insumos y análisis de comprobación). Teniendo en cuenta el contexto operativo, el posible ingreso de contaminantes y el tipo de mecanismo, se fijó en 6 meses el recuento cíclico de partículas. La muestra de aceite una vez extraída, se envía a laboratorio para su análisis el cual tiene un costo de $ 320.00 Aún considerando un reemplazo de la carga de lubricante cada 3 años, los daños que podría ocasionar un exceso de contaminación no controlado por el lapso de 10 años, harían necesario el recambio del conjunto de engranajes, costo que alcanza los $ 16 500.00. Por su parte, reponer la carga lubricante cuesta $ 1 850.00. Dada las características del proceso, reemplazar el reductor ocasionará pérdidas de producción por $ 11 400.00. De los datos y experiencia del personal técnico se sabe que en los últimos 6 años en dos oportunidades el nivel de limpieza 1504406 superó el nivel indicado como límite. Evaluar la conveniencia económica de realizar la tarea predictiva de análisis de aceite.

Es necesario identificar correctamente las variables de este caso, así como los parámetros de evaluación que son controladas mediante la estrategia del mantenimiento predictivo.
El activo a gestionar viene a ser el “reductor de transmisión”, donde el parámetro de evaluación es el nivel de contaminación mediante el conteo de partículas medidas con el código ISO 4406 que es obtenida en un análisis de aceite SOS (Schedule Oil Sampling), siendo el nivel máximo de 18/16/14.
Siendo un programa de mantenimiento predictivo, éste debe tener una frecuencia determinada de ejecución debiendo tener como objetivo el de identificar oportunamente niveles elevados de contaminación para evitar daños mayores en el componente. El costo de esta estrategia dependerá de las técnicas utilizadas, el nivel de competencia del personal requerido y de la cantidad de análisis que se hayan estimado por el departamento de mantenimiento en un tiempo determinado.
Luego de haber identificado las variables, las reemplazamos en la fórmula propuesta para la comparación respectiva.
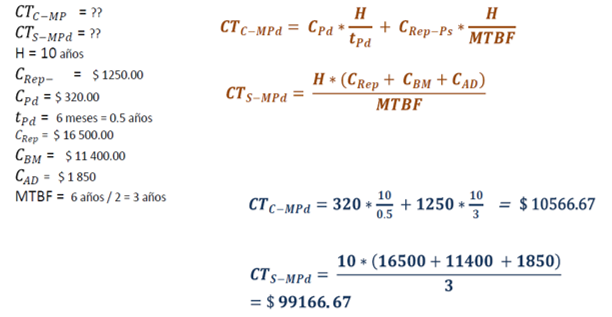
De acuerdo a los resultados, evidentemente será factible y conveniente implementar la estrategia del Mantenimiento Predictivo por el menor impacto económico que se obtiene al compararlo con el mantenimiento correctivo, sin embargo, hay que considerar que para que una organización tenga un área de mantenimiento predictivo efectivo, tendrá que haber logrado dominar y estructurar de manera sistematizada de las estrategias del mantenimiento preventivo y correctivo propiamente dichas.
Las tareas predictivas, podrían convertirse en tareas preventivas si se logra reducir la variabilidad de los tiempos promedios entre fallas (MTBF), esto permitirá realizar proyecciones de presupuestos acorde con la realidad del proceso.
Es de esta manera en cómo se plantea la selección adecuada de la estrategia que permita una gestión optimizada de los activos que se encuentran a cargo del departamento de mantenimiento, como pudimos analizar, no existe una única decisión de selección, sino que dependerá de diversos factores y propuestas de mejora que deberán ser estudiados por el profesional de mantenimiento.